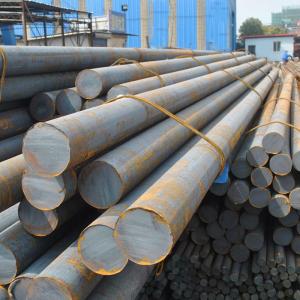
Add to Cart
AISI 8620 Steel is a low alloy nickel, chromium, molybdenum case hardening steel, generally supplied in the as rolled condition with a maximum hardness max HB 255. It is commonly supplied in 8620 round bar.
It is flexible during hardening treatments, thus enabling improvement of case/core properties. Pre hardened and tempered (uncarburized) 8620 can be further surface hardened by nitriding. However, it will not respond satisfactorily to flame or induction hardening due to its low carbon content.
Steel 8620 is suited for applications which require a combination of toughness and wear resistance.
CHEMICAL COMPOSITION
Element | C | Mn | Si | P | S | Mo |
4140 | 0.38~0.43% | 0.75~1.0% | 0.15~0.30% | 0.035% | 0.04% | 0.15~0.25% |
4130 | 0.28~0.33% | 0.70~0.90% | 0.15~0.35% | 0.035% | 0.04% | 0.15~0.25% |
4340 | 0.38%~0.43% | 0.60~0.80% | 0.15~0.35% | 0.035% | 0.04% | 0.20~0.30% |
5140 | 0.38~0.48% | 0.70~0.90% | 0.15~0.35% | 0.035% | 0.04% | - |
8620 | 0.18~0.23% | 0.70~0.90% | 0.15~0.35% | 0.035% | 0.04% | 0.15~0.25% |
HEAT TREATMENT OPTION
FABRICATION AND HEAT TREATMENT
Machinability
Long, gummy chips characterize this alloys machinability. It can be machined in the annealed condition, however condition H1150M will yield best results. Post machining solution treatment of parts will be required prior to final hardening if machining in this condition.
Welding
Successfully welded by common fusion and resistance methods, this alloy should not be joined by oxyacetylene welding. AWS E/ER630 filler metal is recommended if required.
Heat Treatment
CONDITION A--Soak at 1900 F (1038 C) for 30 minutes and cool below 60 F (16 C) for complete martensite transformation. CONDITION H 950- Treat Condition A material at 900 F(482 C) for 1 hour, air cool.. CONDITION H925, H1025, H1075, H1100, H1150- Soak solution treated material for 4 hours at specified temperature, air cool, CONDITION H1150M- Soak solution treated material at 1400 F (760 C) for 2 hours, air cool, then re-heat to 1150 F (620 C) for 4 hours and air cool.
Forging
Soak for 1 hour at 2150 F (1177 C) prior to forging. Do not work below 1850 F (1010 C). Post-work solution treatment is required prior to final hardening.
Stress Relieving
For pre-hardened steel stress relieving is achieved by heating steel 4340 to between 500 to 550°C. Heat to 600 °C – 650 °C, hold until temperature is uniform throughout the section, soak for 1 hour per 25 mm section, and cool in still air.
Annealing
A full anneal may be done at 844°C (1550 F) followed by controlled (furnace) cooling at a rate not faster than 10°C (50 F) per hour down to 315°C (600 F). From 315°C 600 F it may be air cooled.
Tempering
AISI 8620 alloy steel should be in the heat treated or normalized and heat treated condition before tempering. The tempering temperature for depends upon the strength level desired. For strength levels in the 260 – 280 ksi range temper at 232°C (450 F). For strength in the 125 – 200 ksi range temper at 510°C (950 F). And don’t temper the 4340 steels if it is in the 220 – 260 ksi strength range as tempering can result in degradation of impact resistance for this level of strength.
Tempering should be avoided if possible within the range 250 °C – 450 °C due to temper brittleness.